Price: 10.00
Traditional, thermally cured, coil coatings are very flexible paints with good abrasion
resistance and a designed in durability consistent with the end use. The flexibility and
abrasion resistance are very necessary during the post forming operations when the metal
substrate is bent, sometimes quite severely, by high speed processing machines.
Although the coil coating process is already one of the most environmentally friendly of
all painting techniques with the production of low volumes of waste and the
employment of emmission abatement techniques, the industry is continuously striving to
improve efficiency, reduce energy consumption, reduce emissions and run at even higher
line speeds. One method of curing which has elusively offered all of these things to the
coil coater for the past 25 years is radiation curing. The line speeds and volume produced
can justify the investment required. The flat substrate fits snugly with the roller coating
techniques favoured by the radcure industry. Finally the instantaneous nature of cure has
distinct advantages in speed and contolability. So why are there so few, if any, lines
producing high volumes of strip coated with a radiation curable paint? The answer is of
course performance.
There are five major types of conventional topcoat applied to continuous strip, polyesters
account for 55% of the volume sold and PVC plastisols account for 30%. P\TDF
contributes 5% to the total as do poly-urethanes, finally silicon modified polyesters
(SMPs) account for 2%. One of the primary functions of the organic layer is to ensure that
any cracks which are generated in the metal by the forming processes remain sealed and
are isolated from the general environment. The thermoplastic PVC plastisol coatings
stretch easily under stress and fulfil this requirement well. The crosslinked polyester
systems are also capable of stretching sufficiently to maintain their integrity around tight
T bends (0-2) and over Erichsen domes (7-7.5mm). Even the notoriously inflexible SMPs
approach this degree of flexibility without cracking. These cross linked coatings are
supplied and applied as solutions in organic solvents, during the first part of the
temperature ramp these solvents are evaporated off leaving the resin, crosslinker and
pigment behind on the substrate. At temperatures in excess of 150° C a transetherification
reaction between the polyester and a melamine resin is initaited(2), the resulting network is
both tough and flexible at ambient temperatures. The degree of crosslinking is essentially
independent of rheological control.
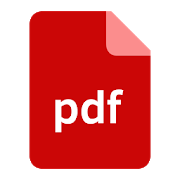
1997 Conference A Thermo-Mechanical Comparison Of Some Electron Beam Formulations With A Thermally Cured Polyester Coil Coating
Order Article