13 October 2013
Year: 2013Price: 10.00
UV Curing is a technology used to cure chemical formulations, such as, adhesives, inks and photo-resists, almost instantly using ultraviolet radiation. The underlying mechanism that enables this is often called “photo-polymerization”. Due to the fact that the curing occurs almost instantaneously, as opposed to minutes/hours when cured by more traditional thermal processes, UV curing is highly conducive to high throughput manufacturing processes. Additionally, reduction of VOC (volatile organic compounds) makes this process environmentally friendly making it further attractive. In this process, monomers, oligomers and other additives, such as, stabilizers, fillers, pigments are mixed in various ratios along with specific photo-initiators. These carefully formulated photo-initiators, designed for a selected UV spectral response band, play an important role in facilitating the photo-polymerization and deliver the desired physical and chemical properties of the cured films. Since it was originally introduced in the 1960's, UV curing has been widely adopted in many industries including automotive, telecommunications, electronics, graphic arts, converting and metal, glass and plastic decorating.
Since its introduction over 50 years ago, UV curing was originally performed using arc lamps. Arc lamps provided a low cost solution for this. However, the primary drawbacks of arc lamps are their limited life time, as well as, unstable spectral output, as the filament materials used to ignite the plasma often interact with the species inside the bulb that causes spectral shift and eventually a failure. Their reduced life time causes significant disruption to manufacturing environments that are very sensitive to production down time.
Since its invention in early 70’s, “electrode-less” lamp technology has revolutionized the industrial UV curing industry. This electrode-less lamp technology used no electrodes, unlike their arc lamp counterparts, thereby eliminating the short life time issue. Additionally, lack of electrodes allowed the flexibility to introduce more elements into the bulb envelopes that generated a multitude of UV spectral output. This further allowed the photo-chemists to develop numerous innovative formulations that revolutionized the industry further.
Since its introduction over 50 years ago, UV curing was originally performed using arc lamps. Arc lamps provided a low cost solution for this. However, the primary drawbacks of arc lamps are their limited life time, as well as, unstable spectral output, as the filament materials used to ignite the plasma often interact with the species inside the bulb that causes spectral shift and eventually a failure. Their reduced life time causes significant disruption to manufacturing environments that are very sensitive to production down time.
Since its invention in early 70’s, “electrode-less” lamp technology has revolutionized the industrial UV curing industry. This electrode-less lamp technology used no electrodes, unlike their arc lamp counterparts, thereby eliminating the short life time issue. Additionally, lack of electrodes allowed the flexibility to introduce more elements into the bulb envelopes that generated a multitude of UV spectral output. This further allowed the photo-chemists to develop numerous innovative formulations that revolutionized the industry further.
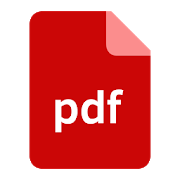
2013 Conference Advancements in microwave powered UV curing system utilizing solid state switch mode power supply
Order Article