Price: 10.00
Over the last decade the irradiance of commercial UV-LED devices increased from a few hundred mW/cm² to approximately 10 W/cm² leading to a wide range of UV-LED curing applications, e.g. curing of adhesives, coatings as well as pinning and full curing of digital inks.
UV-LED sources are characterized by low energy consumption, low voltage, ease of integration, long service life and fast switching, while generating neither heat nor ozone. The narrow band long wavelength emission of UV-LEDs in the UV-A and the lack of shortwave UV-B or UV-C radiation require a reformulation of curing materials. Curing with traditional mercury arc-lamps utilizes shorter wavelengths for surface curing, with no or limited need for oxygen removal by inertization. In order to avoid inertization in UV-LED curing, modification of the photoinitiator composition of a formulation is necessary to make UV-LEDs an alternative for arc-lamps and to benefit from the advantages UV-LED technology can offer.
UV-LED curable inkjet inks have been successfully formulated to match the peak wavelength of 395 nm. These inks show excellent surface and deep cure at considerably lower cure doses. During the last few years commercial high output UV-LEDs with peak wavelengths different from 395 nm, ranging from 365 nm to 405 nm have been introduced. The effect of different wavelengths (395 nm and 365 nm) on deep cure rates has been evaluated using FT-IR spectroscopy [1].
In our study we examine the influence of wavelength, dose and irradiance on curing quality of industrial LED curable inkjet inks including surface cure (without inertization) to explore the opportunity to increase the performance of UV-LED curing systems.
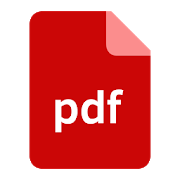
2011 Conference Curing behavior of UVLED curable inks Influence of dose irradiance and wavelength
Order Article