Price: 10.00
The ability of energetic electrons to initiate polymerization reactions has intrigued polymer chemists and engineers for a long time. Early development work was done with low dose rate Co60 gamma sources or very high voltage scanned type electron beam accelerators. Both these high-energy curing options were not suited for commercial applications because of prohibitive capital equipment cost. The development of low energy (150-300kV) EB equipment was considered a breakthrough in the curing technology especially since the oil embargo of the mid-seventies made thermal curing options not as attractive. Large chemical companies jumped at the opportunities to synthesize special raw materials that could be EB curable. Opportunities were cited for various markets like printing (offset lithography), pressure sensitive adhesives, and silicone release coatings to name a few. For most of the applications the end product properties obtained by EB curing were quite unique and superior to products obtained from most other curing methods. See Table: 1. Some very large converters saw the benefits that EB processing brought and widely adapted the technology.
As a result EB technology saw good growth through the eighties. However, this growth was short lived and the rapid growth enjoyed in the eighties stayed quite flat in the nineties. EB processing was restricted to very large converters for niche market applications and did not broadly penetrate industry.The main reasons attributed to this limited growth were as follows: EB equipment was quite large and expensive, especially for cost sensitive industries like flexible packaging and converting. In addition the operation and maintenance cost of these accelerators was quite high. EB equipment generated higher than required electron penetration. These electrons damaged radiation sensitive substrates like PVC (discoloration), cellulose and paper materials (loss of physical properties due to chain scission), and certain polyolefin (off-odor and increase of seal initiation temperatures).
Chemistry suppliers restricted their efforts in developing EB curable chemistry due to lack of an industrial EB accelerator meeting the broader market requirements. Electron beam curable inks, coatings, and adhesives were available but at a premium cost and for certain niche applications. Lack of chemistry, and curing equipment was the main reason for a flat to negative growth of EB processing in the nineties.
The energy of electrons expressed in kV, determines the depth of penetration into a material and thus the thickness of the material that can be dried or cured. New low voltage electron beam systems operating at less than 125 kV first introduced in 1999, enable users to obtain all the benefits of EB curing at a price they can afford. This was because the low voltage EB equipment are approximately half the price of the old high voltage EB units and also consume less power and can result in higher production speeds.
A technology break-through in late 1990’s permitted to realize electron beam processors with accelerating voltage less than 150 kV. Up to this time accelerating voltages of 150kV and higher were used to cure inks, coatings and adhesives less than 20 microns thick. These 150 kV EB units to cure thin materials were quite inefficient, because the effective penetration of 150 kV EB unit was at least 3 X higher. As shown in Fig: 1 at least 90% of the energy is not utilized. It was imperative to operate at low energies. But how remained the question?
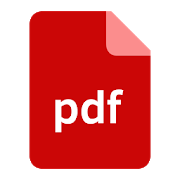
2013 Conference Development in Low Voltage EB Curing For High Product Throughput Applications
Order Article