Price: 10.00
Polyethylene (PE) is the thermoplastic material produced in the largest
quantities in the world. There has been considerable interest in
converting PE to a thermosetting material by crosslinking methods, in
order to combine its low cost, easy processing and good properties with
dimensional stability. It is well known that a modest crosslinking of PE
can considerably improve the thermal stability and the resistance to
electrical discharge, to solvent, to creep and to environmental stresscracking.
In recent years low density (LDPE) and high density (HDPE)
polyethylenes crosslinked to XLPE have become commonly used as
industrial polymers. These products are extensively used for electrical
insulation of wires and cables, hot water piping, heat-shrinkable tubing
and film and as foam. Most commercial XLPE products to date are
produced by two methods: high-energy irradiation (y-rays1 or electron
beam2) and chemical reactions (with peroxides3 or alkoxy silane4 ). The
above methods are now producing millions dollars worth of XLPE
products every year. However, the main shortcomings of high-energy
radiation cros slinking are high primary investment, complicated
operation and processing technology and critical requirement for safety
and radiation protection. Chemical methods have low heat-efficiency,
long crosslinking times and complicated process requirements because of
the critical condition for the crosslinking reactions.
Photoinitiated crosslinking of PE by UV irradiation has been known
since the 1950's when Oster and his co-workers5,6 first reported their
studies. Using UV light in the 200-300 nm range, they found that the.
irradiation time could be decreased by a factor of 1000 when benzophenone
was added as a sensitizer. This simple method of UV light crosslinking
caught a noticeable attention. A number of experimental studies of
photoinitiated crosslinking of PE were published in the following 20
years,7-11 but there was no breakthrough in the commercial application of
UV crosslinking. It is difficult to crosslink thick solid samples of PE
homogeneously because of two main problems: poor penetration of UV
light in bulk PE and slow reaction rate of photocrosslinking of PE. Usually
it takes at least several minutes of UV irradiation to obtain degrees of
crosslinking of practical application; Therefore, UV light crosslinking
has been limited to applications of.photocuring and.other surface
modifications for films less than 0.3 mm thick. The photocrosslinking of
PE has several inherent advantages, however, compared with the two
commercial methods mentioned. For example, UV photocrosslinking is a
one-stage process with inexpensive and simple equipment; there is little
degradation or oxidation of the polymer during the UV crosslinking
process; UV light sources are readily available and easy to handle, and
the investment cost is low. 11 Therefore, photocrosslinking of PE and its
application still attract some researchers 12-15.
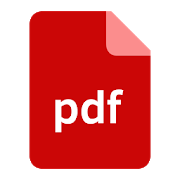
1993 Conference Photocrosslinking Process And Its Industrial Application For The Production Of Thin Wall Insulated Wires
Order Article